Are You Ready for the Next Suez-Level Disruption?
This is a guest post by Jake Rheude.
The core lesson of 2020 and 2021, so far, is that many global supply chains are one bad day away from breaking. An outbreak at a single fulfillment location, a ship stuck in a canal, or an issue discovered during a routine inspection can all grind a supply chain to a halt. Whether or not the dust has settled for your business, there are some core lessons to learn and practices to implement to protect you from the next significant disruption. Here are a few to help you start.
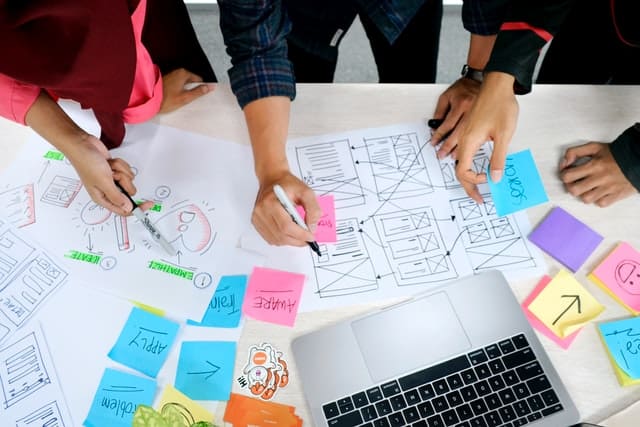
Diversify Every Node
There’s a painfully obvious lesson in much of the recent supply chain disruptions that needs repeating. Diversify your supply chain at every point. Tell your boss and procurement heads, tell your suppliers, and tell your friends and family. Keep spreading this because, while it’s a top safety valve, many companies struggle to implement diversity.
One big issue is that diversity in the supply chain is easy to understand in the abstract but hard to put into practice. And, for many parts, there aren’t great ways to speed up the process. So, instead of thinking about the ideal, here are a few suggestions that a company can pilot to start diversifying its supply chain:
- Find an additional fulfillment partner whose locations are far from your existing partner. Split inventory between them and have them fill the closest orders, such as one on each U.S. coast. For eCommerce, consider testing a new partnership with a pilot for fulfilling your lowest-volume channel.
- Look for a manufacturer that’s local or in a different region from your current provider. Test their capabilities on one or two SKUs that are about to enter their normal seasonal slump, giving you more room for Q&A and the ability to rely on existing safety stock.
- Digitize your documentation and other import activities. Use a standard tool to manage processes — a freight forwarder should be able to point you in the right direction. Use that tool to find additional carriers that are already onboarded. This helps minimize extra activities that diversification can require.
- Use existing software, especially ERP tools, to create small orders for backup suppliers. Have them manage small channels or produce your safety stock. This helps you test a backup or additional supplier before there’s an immediate need.
- Add locations instead of replacing them. Let your partners be additive initially, such as new warehouse locations that utilize on-dock rail services at the Port of Los Angeles, while existing locations are served solely by trucks for this leg. If you had a disruption due to a natural event, such as tornadoes or hurricanes, add distribution centers away from impacted areas.
These steps and others all come with added expense. However, those are the realistic costs of doing business in the era of global supply chains. Even for core functions, multiple partners and locations are your best way to keep operations running and avoid complete disruption.
Understand Your Backups
Finding an alternative or replacement for a process, product, or other supply chain step is the first step. Your second is to create a detailed understanding of what it means to shift these elements, especially if you do so in a crunch.
Some differences are easy to quantify. How much lead time does a secondary manufacturer need? What is your minimum order volume with each partner? Can the trucks of a new carrier partner use your existing loading docks?
Other differences need greater study. When the Suez Canal was blocked, many companies started considering alternate routes like sailing around the southern tip of Africa. According to security experts, both waiting in line at the Suez and taking this alternate route came with increased piracy risks. Companies would need an existing plan that included research on safety and security to make a quick decision. In some instances, delaying a response until you have more data also puts your company, products, or ships at risk.
Don’t Run Too Lean
Through elements such as just-in-time (JIT) manufacturing, lean operations help companies maximize their use of capital. However, it requires everything in a supply chain to run smoothly to generate that benefit.
When something goes wrong, lean often just ends up meaning late.
We saw this before the Suez Canal blockage. During the early months of the COVID-19 pandemic, illnesses and lockdowns disrupted supply chains and manufacturers. Many people and medical settings had a hard time buying protective equipment. Some of that was due to JIT policies that couldn’t handle node loss or scale with demand.
Shipping delays from things like the blockage can compound JIT issues. These bottlenecks generally force a large number of containers to arrive at ports in a short amount of time. That congestion can overwhelm ports and cause further delays as ships must wait to unload. This is one event that creates delays during transit and at import.
The best way for companies to address this issue is to hold more inventory when possible and plan for longer lead times. Create capacity to fill a few more orders so you can meet demand spikes or avoid stockouts during a delay. Thankfully, diversifying your supply chain and shortening it with more local partners can help you mitigate some of these issues as well.
Include a Debrief Phase
It’s incredibly likely that your supply chain and overall business has experienced a disruption. Even if products could move to you freely, there’s a chance you faced shifting customer demand, employee concerns, or even the need to reconfigure warehouse space to create distance between staff. Many companies shifted to outsourcing their fulfillment because of an immediate need caused by such a challenge.
After you’ve taken those immediate responses and worked to get business back on track, it’s important to debrief. Company leadership, managers, and regular employees all need information on what happened, how you responded, and what did or didn’t work. They’ll need your help understanding what can be done better.
Senior leaders should take the lead on reviewing causes and reactions. Have them lead your debriefing by first explaining the goal: understanding what happened, it’s cause, and the impact of the event as well as your decisions. A robust debriefing can help your supply chain team understand and identify future risks, while generating more options to research as your response for the next black swan event.
And, don’t forget one element about debriefing that management researchers say is critical: it’s a way to understand what happened and plan a better response, not find ways to assign blame.
Help Your Customers Respond
One final consideration for developing your company’s response to black swan events is to look outside of your internal policies. Focus on the end-consumer and see what the disruptions look like from their point of view. Are the impact ripples washing in like a low tide or do they feel like a storm surge buffeting the shore?
Help your customers understand the impact and find ways to resolve it. If possible, help them relax and understand that things will be all right. Give reassurance and updated delivery estimates in the same breath.
Everything from the start of the COVID-19 pandemic through the Suze Canal and even the recent Colonial Pipeline disruption has been a reminder that supply chains run their lives. Each disruption highlights the fragility of their plan on any given day. Assist them in getting through these events. By being a comforting presence, they’re more likely to return to your storefront, digital or brick-and-mortar, when the seas settle.
This was a guest post by Jake Rheude.
Author Bio
Jake Rheude is the Director of Marketing for Red Stag Fulfillment, an ecommerce fulfillment warehouse that was born out of ecommerce. He has years of experience in ecommerce and business development. In his free time, Jake enjoys reading about business and sharing his own experience with others.